ग्राइंडिंग डिस्क विभिन्न उद्योगों में महत्वपूर्ण भूमिका निभाते हैं, जो सामग्री को आकार देने और परिष्करण में सहायता करते हैं। हालांकि, किसी भी अन्य उपकरण की तरह, वे उन समस्याओं से मुक्त नहीं हैं जो उनकी दक्षता और प्रदर्शन को बाधित कर सकती हैं। इस लेख में, हम ग्राइंडिंग डिस्क से जुड़ी आम समस्याओं पर चर्चा करेंगे, उनके मूल कारणों का पता लगाएंगे और निर्बाध वर्कफ़्लो के लिए प्रभावी समाधान प्रदान करेंगे।
परिचय
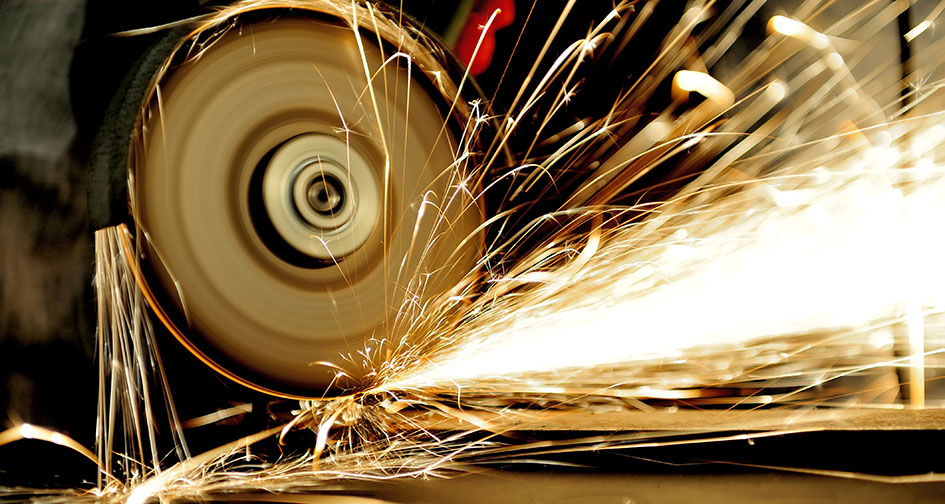
ग्राइंडिंग डिस्क विभिन्न उद्योगों में एक मौलिक भूमिका निभाते हैं, जो सामग्री हटाने, आकार देने और परिष्करण प्रक्रियाओं के लिए आवश्यक उपकरण के रूप में कार्य करते हैं। उनकी परिभाषा, उद्योगों में महत्व और सामना किए जाने वाले आम मुद्दों को समझना उनके उपयोग को अनुकूलित करने और कुशल संचालन सुनिश्चित करने के लिए महत्वपूर्ण है।
ए. ग्राइंडिंग डिस्क की परिभाषा
पीसने वाली डिस्क घर्षण उपकरण हैं जिनका उपयोग मशीनिंग प्रक्रियाओं में सामग्री की सतहों को काटने, पीसने या चमकाने के लिए किया जाता है। ये डिस्क आम तौर पर घर्षण कणों से बनी होती हैं जो एक बैकिंग सामग्री से जुड़ी होती हैं, जिससे एक घूमने वाला उपकरण बनता है जो अतिरिक्त सामग्री को हटा सकता है, सतहों को चिकना कर सकता है या किनारों को तेज कर सकता है। वे विभिन्न आकृतियों और आकारों में आते हैं, जिनमें से प्रत्येक को विशिष्ट अनुप्रयोगों के लिए डिज़ाइन किया गया है।
बी. विभिन्न उद्योगों में महत्व
धातु उद्योग:
धातु निर्माण और विनिर्माण में, धातु की सतहों को आकार देने, उन्हें खुरचने और परिष्कृत करने के लिए पीसने वाली डिस्क महत्वपूर्ण होती हैं। सटीक आयाम और सतह की गुणवत्ता प्राप्त करने के लिए आमतौर पर इन्हें एंगल ग्राइंडर के साथ उपयोग किया जाता है।
निर्माण उद्योग:
निर्माण पेशेवर कंक्रीट की सतह तैयार करने, खुरदुरे किनारों को चिकना करने, तथा पत्थर और कंक्रीट जैसी सामग्रियों में खामियों को दूर करने जैसे कार्यों के लिए पीसने वाली डिस्क पर भरोसा करते हैं।
मोटर वाहन उद्योग:
ऑटोमोटिव क्षेत्र में औजारों को तेज करने से लेकर धातु के घटकों को आकार देने और परिष्करण करने तक के कार्यों के लिए ग्राइंडिंग डिस्क आवश्यक हैं। वे ऑटोमोटिव भागों की सटीकता और गुणवत्ता में योगदान करते हैं।
लकड़ी का काम उद्योग:
लकड़ी के कारीगर लकड़ी की सतहों को आकार देने और चिकना करने के लिए पीसने वाली डिस्क का उपयोग करते हैं। ये डिस्क अतिरिक्त सामग्री को हटाने, आकृतियों को परिष्कृत करने और आगे की परिष्करण के लिए लकड़ी को तैयार करने में प्रभावी हैं।
सामान्य विनिर्माण:
ग्राइंडिंग डिस्क का उपयोग विभिन्न विनिर्माण प्रक्रियाओं में किया जाता है, जहां सटीक सामग्री निष्कासन की आवश्यकता होती है, जिससे उच्च गुणवत्ता वाले घटकों के उत्पादन में योगदान मिलता है।
सी. आम तौर पर सामना किए जाने वाले मुद्दे
डिस्क घिसाव और घर्षण:
लगातार इस्तेमाल से ग्राइंडिंग डिस्क घिस सकती है और घिस सकती है, जिससे उसका प्रदर्शन प्रभावित हो सकता है। दक्षता बनाए रखने के लिए नियमित निरीक्षण और प्रतिस्थापन आवश्यक है।
अत्यधिक गर्मी:
लंबे समय तक उपयोग के दौरान अत्यधिक घर्षण से डिस्क अधिक गर्म हो सकती है, जिससे डिस्क की स्थायित्व और तैयार सतह की गुणवत्ता प्रभावित हो सकती है। उचित शीतलन उपाय और समय-समय पर ब्रेक लेना आवश्यक है।
रुकावट:
पीसने वाली डिस्क पर सामग्री के अवशेष जमा हो सकते हैं, जिससे उनकी प्रभावशीलता कम हो जाती है। नियमित सफाई या एंटी-क्लॉगिंग सुविधाओं वाली डिस्क चुनने से इस समस्या को रोकने में मदद मिलती है।
कंपन और डगमगाहट:
असंतुलन या असमान घिसाव के कारण कंपन या डगमगाहट हो सकती है, जिससे फिनिश की गुणवत्ता और संचालन की सुरक्षा दोनों पर असर पड़ सकता है। उचित स्थापना और संतुलन महत्वपूर्ण हैं।
गलत डिस्क चयन:
किसी विशिष्ट सामग्री या अनुप्रयोग के लिए गलत प्रकार की ग्राइंडिंग डिस्क चुनने से अकुशलता और संभावित क्षति हो सकती है। सामग्री अनुकूलता के आधार पर उचित चयन आवश्यक है।
ग्राइंडिंग डिस्क से जुड़ी परिभाषा, महत्व और संभावित चुनौतियों को समझना इन उपकरणों पर निर्भर उद्योगों के लिए आवश्यक है। आम मुद्दों को संबोधित करके और उचित उपयोग सुनिश्चित करके, उद्योग अपने संबंधित अनुप्रयोगों में ग्राइंडिंग डिस्क की प्रभावशीलता को अधिकतम कर सकते हैं।
पीसने वाली डिस्क पर टूट-फूट
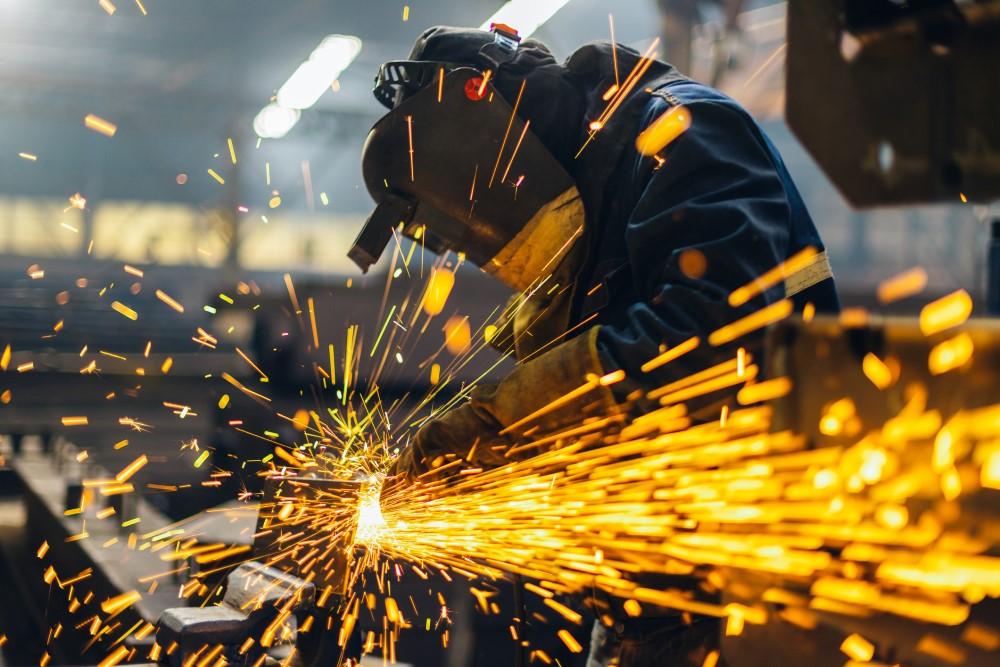
पीसने वाली डिस्क विभिन्न उद्योगों में आवश्यक उपकरण हैं, जो धातु निर्माण से लेकर कंक्रीट पॉलिशिंग तक के कार्यों के लिए आवश्यक घर्षण प्रदान करते हैं। पीसने वाली डिस्क पर घिसाव और टूट-फूट में योगदान देने वाले कारकों को समझना उनके प्रदर्शन को अनुकूलित करने और सुरक्षा सुनिश्चित करने के लिए महत्वपूर्ण है।
सामग्री कठोरता और संरचना:
कठोरता भिन्नता:पीसने वाली डिस्क अलग-अलग कठोरता स्तरों वाली सामग्रियों का सामना करती है। धातु और कंक्रीट जैसी घर्षण सामग्री कठोरता में काफी भिन्न हो सकती है। कठोर सामग्रियों के खिलाफ लगातार पीसने से घिसाव तेज हो जाता है।
सामग्री की संरचना:पीसने वाली सामग्री में घर्षण तत्वों की उपस्थिति पीसने वाली डिस्क पर घिसाव को प्रभावित कर सकती है। घर्षण कण डिस्क के घिसाव को तेज कर सकते हैं।
पीसने का दबाव और बल:
अत्यधिक दबाव:ग्राइंडिंग डिस्क पर अत्यधिक दबाव डालने से यह जल्दी घिस सकती है। डिस्क पर अनावश्यक तनाव से बचने के लिए विशिष्ट अनुप्रयोग के लिए अनुशंसित दबाव का उपयोग करना आवश्यक है।
अपर्याप्त बल: दूसरी ओर, अपर्याप्त बल के कारण लंबे समय तक घर्षण हो सकता है, जिससे अतिरिक्त घर्षण और गर्मी उत्पन्न हो सकती है, जिससे घिसाव बढ़ सकता है।
डिस्क की गुणवत्ता और संरचना:
अपघर्षक सामग्री की गुणवत्ता:पीसने वाली डिस्क में इस्तेमाल की जाने वाली घर्षण सामग्री की गुणवत्ता उसके जीवनकाल को काफी हद तक प्रभावित करती है। उच्च गुणवत्ता वाली घर्षण सामग्री घिसाव का प्रतिरोध करती है और लंबे समय तक तीक्ष्णता बनाए रखती है।
बॉन्डिंग एजेंट:घर्षण कणों को एक साथ रखने वाला बॉन्डिंग एजेंट एक महत्वपूर्ण भूमिका निभाता है। एक अच्छी तरह से डिज़ाइन किया गया बॉन्डिंग एजेंट डिस्क की स्थायित्व को बढ़ाता है।
कार्य वातावरण की स्थितियाँ:
तापमान:पीसने के दौरान उत्पन्न उच्च तापमान डिस्क की संरचना को प्रभावित कर सकता है। अत्यधिक गर्मी बॉन्डिंग एजेंट को कमजोर कर देती है और घिसाव को तेज कर देती है।
नमी और प्रदूषक:कार्य वातावरण में नमी या संदूषकों के संपर्क में आने से ग्राइंडिंग डिस्क की अखंडता प्रभावित हो सकती है, जिससे वह तेजी से खराब हो सकती है।
ऑपरेटर तकनीक:
उचित तकनीक:ऑपरेटर कौशल और तकनीक महत्वपूर्ण हैं। अनुचित उपयोग, जैसे गलत कोण पर पीसना या अत्यधिक बल का उपयोग करना, असमान घिसाव में योगदान दे सकता है और डिस्क की लंबी उम्र को कम कर सकता है।
नियमित निरीक्षण:ऑपरेटरों को नियमित रूप से ग्राइंडिंग डिस्क का निरीक्षण करना चाहिए ताकि किसी भी तरह के नुकसान या घिसाव के लक्षण न दिखें। एक निश्चित सीमा से ज़्यादा घिसाव दिखाने वाली डिस्क को तुरंत बदल देना चाहिए।
डिस्क आकार और RPM संगतता:
सही आकार:ग्राइंडर के लिए सही आकार की डिस्क का उपयोग करना बहुत ज़रूरी है। गलत आकार की डिस्क असमान रूप से घिस सकती हैं या सुरक्षा जोखिम पैदा कर सकती हैं।
आरपीएम संगतता:पीसने वाली डिस्क के लिए अनुशंसित प्रति मिनट चक्कर (आरपीएम) का पालन करने से इष्टतम प्रदर्शन सुनिश्चित होता है और समय से पहले घिसाव से बचाव होता है।
नियमित रखरखाव, अनुशंसित परिचालन स्थितियों का पालन, और कार्य के लिए सही पीसने वाली डिस्क का चयन करना घिसाव और टूट-फूट को कम करने के लिए आवश्यक अभ्यास हैं। घिसाव को प्रभावित करने वाले कारकों को समझकर, ऑपरेटर पीसने वाली डिस्क की दीर्घायु और दक्षता को बढ़ा सकते हैं, जिससे सुरक्षित और अधिक उत्पादक पीसने वाले संचालन में योगदान मिलता है।
असमान पीस
असमान पीसने से तात्पर्य ऐसी स्थिति से है, जहाँ पीसने वाली सतह पर एक समान और चिकनी फिनिश नहीं मिलती है। यह समस्या विभिन्न कारणों से उत्पन्न हो सकती है और वर्कपीस की गुणवत्ता को प्रभावित कर सकती है। असमान पीसने में योगदान देने वाले सामान्य कारक और संभावित समाधान इस प्रकार हैं:
गलत पीस पहिया चयन:
समाधान:सुनिश्चित करें कि पीसने वाला पहिया पीसने वाली सामग्री के लिए उपयुक्त है। विभिन्न सामग्रियों को विशिष्ट घर्षण गुणों की आवश्यकता होती है। आवेदन के लिए सही पहिया प्रकार, ग्रिट आकार और बॉन्ड चुनें।
अनुचित व्हील ड्रेसिंग:
कारण:यदि पीसने वाले पहिये को ठीक से तैयार नहीं किया गया है तो इससे असमान घिसाव और अप्रभावी कटाई हो सकती है।
समाधान:पीसने वाले पहिये को नियमित रूप से ड्रेसिंग करें ताकि उसका आकार बना रहे और उसमें जमा हुआ मलबा हट जाए। उचित ड्रेसिंग से एक समान कटिंग सतह सुनिश्चित होती है।
अपर्याप्त पीसने वाला द्रव या शीतलक:
कारण:पीसने वाले तरल पदार्थ के अपर्याप्त या अनुचित उपयोग के परिणामस्वरूप घर्षण और गर्मी बढ़ सकती है, जिससे असमान पीसने की समस्या हो सकती है।
समाधान:गर्मी को दूर करने और घर्षण को कम करने के लिए उपयुक्त पीसने वाले द्रव या शीतलक का उपयोग करें। समान परिणाम प्राप्त करने के लिए उचित शीतलन आवश्यक है।
गलत पीस पैरामीटर:
कारण:अत्यधिक गति, फीड दर या कट की गहराई जैसे गलत पीस मापदंडों का उपयोग करने से असमान पीस हो सकती है।
समाधान:सामग्री और अनुप्रयोग आवश्यकताओं के अनुसार पीसने के मापदंडों को समायोजित करें। इष्टतम सेटिंग्स के लिए निर्माता की सिफारिशों का संदर्भ लें।
घिसा हुआ पीसने वाला पहिया:
कारण:घिसा हुआ पीसने वाला पहिया एक समान काटने वाली सतह प्रदान नहीं कर सकता है, जिसके परिणामस्वरूप असमान पीसने की क्रिया होती है।
समाधान:जब पीसने वाले पहिये का उपयोग करने लायक जीवन समाप्त हो जाए तो उसे बदल दें। घिसाव के संकेतों के लिए नियमित रूप से पहिये का निरीक्षण करें।
असमान दबाव या फ़ीड दर:
कारण:पीसने के दौरान असमान दबाव या असंगत फीड दर के कारण सामग्री का निष्कासन अनियमित हो सकता है।
समाधान:एकसमान दबाव लागू करें और पूरे वर्कपीस में एक समान फीड दर बनाए रखें। ऑपरेटर कौशल और विवरण पर ध्यान देना महत्वपूर्ण है।
मशीन संबंधी समस्याएं:
कारण:पीसने की मशीन में यांत्रिक समस्याएं, जैसे कि गलत संरेखण या धुरी से संबंधित समस्याएं, असमान पीसने का कारण बन सकती हैं।
समाधान:पीसने वाली मशीन पर नियमित रखरखाव जाँच करें। उचित कार्यक्षमता सुनिश्चित करने के लिए किसी भी यांत्रिक समस्या का तुरंत समाधान करें।
वर्कपीस फिक्सचरिंग:
कारण:खराब तरीके से सुरक्षित या गलत संरेखित वर्कपीस के कारण असमान पीस हो सकती है।
समाधान:वर्कपीस की उचित स्थिरता और संरेखण सुनिश्चित करें। पीसने की प्रक्रिया के दौरान हिलने से रोकने के लिए इसे कसकर सुरक्षित करें।
असमान पीसने से निपटने के लिए उचित उपकरण सेटअप, सही संचालन पैरामीटर और नियमित रखरखाव प्रथाओं के संयोजन की आवश्यकता होती है। ऑपरेटरों को पीसने के अनुप्रयोगों में उच्च-गुणवत्ता और सुसंगत परिणाम प्राप्त करने के लिए समस्याओं की तुरंत पहचान करने और उन्हें ठीक करने के लिए प्रशिक्षित किया जाना चाहिए। नियमित निरीक्षण और सर्वोत्तम प्रथाओं का पालन पीसने की प्रक्रिया के दौरान कुशल और समान सामग्री हटाने में योगदान देता है।
ओवरहीटिंग की समस्या
पीसने के दौरान ज़्यादा गरम होना एक आम समस्या है जो पीसने वाले पहिये और वर्कपीस दोनों के प्रदर्शन को प्रभावित कर सकती है। अत्यधिक गर्मी से कई तरह की समस्याएं हो सकती हैं, जिसमें पहिये का जीवन कम होना, वर्कपीस को थर्मल क्षति और कुल मिलाकर पीसने की क्षमता में कमी शामिल है। यहाँ ओवरहीटिंग की समस्याओं को संबोधित करने के संभावित कारण और समाधान दिए गए हैं:
गलत पीस पैरामीटर:
कारण:अनुचित पीस मापदंडों का उपयोग, जैसे अत्यधिक गति, फीड दर, या कट की गहराई, से अत्यधिक गर्मी उत्पन्न हो सकती है।
समाधान:पीसने के मापदंडों को अनुशंसित सीमा के भीतर समायोजित करें। पीसने वाली सामग्री के आधार पर इष्टतम सेटिंग के लिए निर्माता के दिशा-निर्देशों से परामर्श करें।
अपर्याप्त शीतलन या स्नेहन:
कारण:शीतलक या पीसने वाले द्रव के अपर्याप्त उपयोग के परिणामस्वरूप घर्षण और गर्मी बढ़ सकती है।
समाधान:पीसने की प्रक्रिया के दौरान शीतलक या स्नेहक की पर्याप्त आपूर्ति सुनिश्चित करें। उचित शीतलन गर्मी को नष्ट करने और थर्मल क्षति को रोकने में मदद करता है।
गलत पहिया चयन:
कारण:पीसने वाली सामग्री के लिए अनुपयुक्त विनिर्देशों वाले पीसने वाले पहिये का चयन करने से अधिक गर्मी उत्पन्न हो सकती है।
समाधान:विशिष्ट अनुप्रयोग के लिए सही अपघर्षक प्रकार, ग्रिट आकार और बॉन्ड के साथ पीसने वाले पहिये का चयन करें। सामग्री के साथ पहिये का मिलान करने से गर्मी का उत्पादन कम होता है।
वर्कपीस सामग्री संबंधी मुद्दे:
कारण:कुछ सामग्रियां, विशेषकर जिनकी तापीय चालकता खराब होती है, पीसने के दौरान अधिक गर्म होने की संभावना होती है।
समाधान:कम तापीय चालकता वाली सामग्रियों के लिए पीसने के मापदंडों को समायोजित करें। गर्मी के प्रति संवेदनशील सामग्रियों के लिए डिज़ाइन किए गए विशेष पीसने वाले पहिये का उपयोग करने पर विचार करें।
व्हील ड्रेसिंग समस्याएं:
कारण:पीसने वाले पहिये की अनियमितता या अनुचित ड्रेसिंग के कारण असमान संपर्क और गर्मी का निर्माण हो सकता है।
समाधान:पीसने वाले पहिये को नियमित रूप से सजाते रहें ताकि उसका आकार बना रहे और उसमें जमा हुआ कोई भी चमकीला पदार्थ या मलबा हट जाए। उचित रूप से सजाए गए पहिये निरंतर पीसने का प्रदर्शन सुनिश्चित करते हैं।
अपर्याप्त मशीन रखरखाव:
कारण:खराब रखरखाव वाली पीसने वाली मशीनें अधिक गर्म होने की समस्या उत्पन्न कर सकती हैं।
समाधान:पीसने वाली मशीन पर नियमित रखरखाव करें, जिसमें शीतलक प्रणालियों की जाँच, व्हील ड्रेसिंग उपकरण का निरीक्षण और उचित संरेखण सुनिश्चित करना शामिल है। किसी भी यांत्रिक समस्या का तुरंत समाधान करें।
अपर्याप्त पहिया शीतलक प्रवाह:
कारण:पीसने वाले क्षेत्र में अपर्याप्त शीतलक प्रवाह के परिणामस्वरूप ऊष्मा क्षय कम हो सकता है।
समाधान:शीतलक वितरण प्रणाली की जाँच करें और उसे अनुकूलित करें। सुनिश्चित करें कि शीतलन दक्षता बनाए रखने के लिए शीतलक प्रभावी रूप से पीसने वाले क्षेत्र तक पहुँचता है।
अत्यधिक पीसने का समय:
कारण:बिना ब्रेक के लंबे समय तक पीसने से गर्मी पैदा हो सकती है।
समाधान:बीच-बीच में पीसते रहें और अत्यधिक गर्मी के संचय को रोकने के लिए बीच-बीच में ब्रेक दें। यह तरीका खास तौर पर बड़े या चुनौतीपूर्ण पीसने के कामों के लिए महत्वपूर्ण है।
पीसने में अत्यधिक गर्मी की समस्याओं को संबोधित करने के लिए उचित उपकरण सेटअप, उपयुक्त पीसने के मापदंडों और नियमित रखरखाव प्रथाओं को शामिल करते हुए एक व्यापक दृष्टिकोण की आवश्यकता होती है। ऑपरेटरों को इष्टतम प्रदर्शन, विस्तारित उपकरण जीवन और उच्च गुणवत्ता वाले परिणाम सुनिश्चित करने के लिए पीसने की प्रक्रिया के दौरान गर्मी उत्पादन की निगरानी और नियंत्रण करना चाहिए।
कंपन संबंधी चिंताएँ
पीसने के दौरान अत्यधिक कंपन से कई तरह की समस्याएं हो सकती हैं, जिसमें सतह की गुणवत्ता में कमी, उपकरण का अधिक घिसाव और पीसने वाली मशीन को संभावित नुकसान शामिल है। सटीक और कुशल पीसने की प्रक्रिया को प्राप्त करने के लिए कंपन संबंधी चिंताओं को संबोधित करना महत्वपूर्ण है। कंपन की समस्याओं को कम करने के लिए संभावित कारण और समाधान यहां दिए गए हैं:
असमान पहिया घिसाव:
कारण:पीसने वाले पहिये पर अनियमित घिसाव के कारण कार्यवस्तु के साथ असमान संपर्क हो सकता है, जिससे कंपन उत्पन्न हो सकता है।
समाधान:पीसने वाले पहिये की नियमित रूप से जांच करें और उसे समतल सतह पर रखें। पहिये का उचित रखरखाव कंपन को कम करने में मदद करता है।
असंतुलित पीस पहिया:
कारण:पीसने वाले पहिये में असंतुलन, चाहे असमान घिसाव या विनिर्माण दोष के कारण हो, कंपन पैदा कर सकता है।
समाधान:व्हील बैलेंसर का उपयोग करके ग्राइंडिंग व्हील को संतुलित करें। संतुलन बनाने से वजन का समान वितरण सुनिश्चित होता है और संचालन के दौरान कंपन कम होता है।
अपर्याप्त मशीन अंशांकन:
कारण:मशीन के घटकों, जैसे कि पहिये की धुरी या कार्य-तालिका, का खराब अंशांकन या गलत संरेखण कंपन का कारण बन सकता है।
समाधान:उचित कार्यक्षमता सुनिश्चित करने के लिए मशीन घटकों को नियमित रूप से कैलिब्रेट और संरेखित करें। मशीन सेटअप और संरेखण के लिए निर्माता के दिशानिर्देशों का पालन करें।
कार्य-वस्तु असंतुलन:
कारण:असमान या अनुचित तरीके से सुरक्षित कार्य-वस्तु असंतुलन पैदा कर सकती है और कंपन उत्पन्न कर सकती है।
समाधान:वर्कपीस को ठीक से सुरक्षित करें, सुनिश्चित करें कि यह समान रूप से स्थित और क्लैंप किया गया है। पीसने की प्रक्रिया शुरू करने से पहले किसी भी असंतुलन के मुद्दों को संबोधित करें।
गलत पहिया चयन:
कारण:अनुपयुक्त विनिर्देशों वाले पीसने वाले पहिये का उपयोग करने से कंपन उत्पन्न हो सकता है।
समाधान:पीसने वाली सामग्री के लिए सही अपघर्षक प्रकार, ग्रिट आकार और बॉन्ड के साथ पीसने वाला पहिया चुनें। अनुप्रयोग के लिए पहिया का मिलान करने से कंपन कम हो जाता है।
मशीन की टूट-फूट:
कारण:मशीन के घिसे हुए या क्षतिग्रस्त घटक, जैसे कि बेयरिंग या स्पिंडल, कंपन का कारण बन सकते हैं।
समाधान:नियमित रूप से मशीन के खराब हो चुके भागों का निरीक्षण करें और उन्हें बदलें। उचित रखरखाव अत्यधिक कंपन को रोकने में मदद करता है और पीसने वाली मशीन के जीवन को बढ़ाता है।
अपर्याप्त शीतलक प्रवाह:
कारण:पीसने वाले क्षेत्र में अपर्याप्त शीतलक प्रवाह के परिणामस्वरूप गर्मी का निर्माण और कंपन हो सकता है।
समाधान:उचित शीतलन सुनिश्चित करने के लिए शीतलक वितरण प्रणाली को अनुकूलित करें। प्रभावी शीतलन तापीय विस्तार और संकुचन के जोखिम को कम करता है, जिससे कंपन हो सकता है।
टूल होल्डर संबंधी समस्याएं:
कारण:टूल होल्डर या स्पिंडल इंटरफ़ेस में समस्या होने से कंपन उत्पन्न हो सकता है।
समाधान:सुनिश्चित करें कि टूल होल्डर सुरक्षित रूप से माउंट किया गया है और स्पिंडल के साथ ठीक से संरेखित है। कंपन को कम करने के लिए उच्च गुणवत्ता वाले और ठीक से बनाए गए टूल होल्डर का उपयोग करें।
मशीन फाउंडेशन:
कारण:मशीन की खराब नींव या अपर्याप्त समर्थन कंपन को बढ़ा सकता है।
समाधान:सुनिश्चित करें कि पीसने वाली मशीन स्थिर और उचित रूप से डिज़ाइन की गई नींव पर स्थापित है। मशीन में संचारित कंपन को कम करने के लिए किसी भी संरचनात्मक मुद्दे को संबोधित करें।
पीसने में कंपन संबंधी चिंताओं को प्रभावी ढंग से संबोधित करने के लिए उचित मशीन रखरखाव, पहिया चयन और वर्कपीस हैंडलिंग के संयोजन की आवश्यकता होती है। ऑपरेटरों को समस्याओं की पहचान करने और उन्हें तुरंत हल करने के लिए नियमित निरीक्षण और रखरखाव प्रथाओं को लागू करना चाहिए, जिसके परिणामस्वरूप पीसने का प्रदर्शन और गुणवत्ता में सुधार होगा।
पीसने में लोडिंग संबंधी समस्याएँ
पीसने में लोडिंग से तात्पर्य उस घटना से है जिसमें पीसने वाले पहिये पर घर्षण करने वाले दानों के बीच की जगह पीसने वाली सामग्री से भर जाती है, जिसके परिणामस्वरूप काटने की क्रिया कम हो जाती है और घर्षण बढ़ जाता है। लोडिंग पीसने की प्रक्रिया की दक्षता और गुणवत्ता पर नकारात्मक प्रभाव डाल सकती है। लोडिंग समस्याओं को संबोधित करने के लिए संभावित कारण और समाधान यहां दिए गए हैं:
नरम वर्कपीस सामग्री:
कारण:नरम पदार्थों को पीसने से घर्षणकारी कण तेजी से अवरुद्ध हो सकते हैं।
समाधान:नरम सामग्री पर काम करते समय मोटे ग्रिट और खुली संरचना वाले पीसने वाले पहिये का उपयोग करें। यह त्वरित लोडिंग को रोकने में मदद करता है और कुशल चिप हटाने की अनुमति देता है।
सामग्री संदूषण:
कारण:कार्य-वस्तु सामग्री में उपस्थित संदूषक, जैसे तेल, ग्रीस या शीतलक अवशेष, लोडिंग में योगदान कर सकते हैं।
समाधान:पीसने से पहले दूषित पदार्थों को हटाने के लिए वर्कपीस की उचित सफाई सुनिश्चित करें। लोडिंग को कम करने के लिए उचित कटिंग तरल पदार्थ या शीतलक का उपयोग करें।
गलत शीतलक अनुप्रयोग:
कारण:शीतलक का अपर्याप्त या अनुचित उपयोग अपर्याप्त स्नेहन और शीतलन का कारण बन सकता है, जिसके परिणामस्वरूप लोडिंग हो सकती है।
समाधान:शीतलक प्रवाह और सांद्रता को अनुकूलित करें। सुनिश्चित करें कि शीतलक प्रभावी रूप से पीसने वाले क्षेत्र तक पहुँचता है ताकि प्रक्रिया को चिकना और ठंडा किया जा सके, जिससे लोडिंग को रोका जा सके।
अपर्याप्त पहिया तीक्ष्णता:
कारण:सुस्त या घिसे हुए पीसने वाले पहिये अधिक भार के प्रति संवेदनशील होते हैं, क्योंकि वे अपनी काटने की क्षमता खो देते हैं।
समाधान:पीसने वाले पहिये की तीक्ष्णता बनाए रखने के लिए उसे नियमित रूप से तैयार और धारदार रखें। ताजा घर्षण वाले दानों को उजागर करने और काटने की क्रिया को बढ़ाने के लिए व्हील ड्रेसर का उपयोग करें।
कम पहिया गति:
कारण:पीसने वाले पहिये को कम गति पर चलाने से चिप्स को बाहर निकालने के लिए पर्याप्त केन्द्रापसारी बल उपलब्ध नहीं हो पाता, जिसके कारण लोडिंग होती है।
समाधान:सुनिश्चित करें कि पीसने वाली मशीन विशिष्ट पहिये और वर्कपीस संयोजन के लिए अनुशंसित गति पर काम करती है। उच्च गति बेहतर चिप हटाने में मदद कर सकती है।
अत्यधिक दबाव:
कारण:पीसने के दौरान बहुत अधिक दबाव डालने से सामग्री पहिये में चली जाती है, जिससे भार बढ़ जाता है।
समाधान:मध्यम और सुसंगत पीसने वाले दबाव का उपयोग करें। फ़ीड दर को समायोजित करें ताकि पहिया अत्यधिक दबाव के बिना कुशलतापूर्वक काट सके जिससे लोडिंग हो।
गलत पहिया विनिर्देश:
कारण:पीसने वाली सामग्री के लिए गलत विनिर्देशों वाले पीसने वाले पहिये का उपयोग करने से लोडिंग हो सकती है।
समाधान:विशिष्ट अनुप्रयोग के लिए उपयुक्त अपघर्षक प्रकार, ग्रिट आकार और बॉन्ड के साथ पीसने वाले पहिये का चयन करें। सामग्री के साथ पहिये का मिलान करने से लोडिंग को रोकने में मदद मिलती है।
अपर्याप्त शीतलक सफाई:
कारण:दूषित या पुराना शीतलक लोडिंग संबंधी समस्याओं का कारण बन सकता है।
समाधान:दूषित पदार्थों के जमाव को रोकने के लिए नियमित रूप से कूलेंट को साफ करें और बदलें। ताजा और साफ कूलेंट चिकनाई और शीतलन को बढ़ाता है, जिससे लोडिंग की संभावना कम हो जाती है।
अनुचित ड्रेसिंग तकनीक:
कारण:पीसने वाले पहिये की गलत ड्रेसिंग से अनियमितताएं और लोडिंग हो सकती है।
समाधान:उचित ड्रेसिंग टूल का उपयोग करके पहिये को ठीक से तैयार करें। सुनिश्चित करें कि पहिया प्रोफ़ाइल एक समान है और लोडिंग को रोकने के लिए अनियमितताओं से मुक्त है।
लोडिंग समस्याओं को प्रभावी ढंग से संबोधित करने के लिए उचित व्हील चयन, मशीन सेटअप और रखरखाव प्रथाओं का संयोजन शामिल है। ऑपरेटरों को अनुशंसित प्रक्रियाओं का पालन करना चाहिए, उपयुक्त पीस मापदंडों का उपयोग करना चाहिए, और लोडिंग को कम करने और पीसने के प्रदर्शन को अनुकूलित करने के लिए नियमित व्हील ड्रेसिंग को लागू करना चाहिए।
विभिन्न धातुकर्म और निर्माण अनुप्रयोगों में इष्टतम परिणाम प्राप्त करने के लिए सही ग्राइंडिंग डिस्क का चयन करना महत्वपूर्ण है। चयन काम की जाने वाली सामग्री, वांछित फिनिश और उपयोग किए जा रहे ग्राइंडर के प्रकार जैसे कारकों पर निर्भर करता है।
सही ग्राइंडिंग डिस्क का चयन
सामग्री संगतता:
लौह धातुएँ (इस्पात, लोहा):विशेष रूप से लौह धातुओं के लिए डिज़ाइन की गई पीसने वाली डिस्क का उपयोग करें। इन डिस्क में अक्सर स्टील की कठोरता के लिए उपयुक्त अपघर्षक होते हैं और लोड होने की संभावना कम होती है।
अलौह धातुएँ (एल्यूमीनियम, पीतल):नरम धातुओं के लिए उपयुक्त अपघर्षक युक्त डिस्क चुनें ताकि रुकावट को रोका जा सके। एल्युमिनियम ऑक्साइड या सिलिकॉन कार्बाइड डिस्क आम विकल्प हैं।
घर्षण सामग्री:
एल्युमिनियम ऑक्साइड:लौह धातुओं पर सामान्य प्रयोजन पीसने के लिए उपयुक्त। यह टिकाऊ और बहुमुखी है।
ज़िरकोनिया एल्युमिना:यह उच्चतर काटने की दक्षता और दीर्घायु प्रदान करता है, जिससे यह लौह और अलौह धातुओं पर आक्रामक पीसने के लिए उपयुक्त हो जाता है।
सिलिकन कार्बाइड:अलौह धातुओं और पत्थरों को पीसने के लिए आदर्श। यह एल्युमिनियम ऑक्साइड की तुलना में ज़्यादा तेज़ है लेकिन कम टिकाऊ है।
ग्रिट आकार:
मोटा ग्रिट (24-36):तेजी से स्टॉक हटाने और भारी शुल्क पीस।
मध्यम ग्रिट (40-60):स्टॉक हटाने और सतह परिष्करण में संतुलन बनाए रखता है।
फाइन ग्रिट (80-120):सतह की तैयारी और हल्की पीसने के लिए उपयुक्त, एक चिकनी फिनिश प्रदान करता है।
पहिये का प्रकार:
प्रकार 27 (अवसादित केंद्र):सपाट सतह के साथ मानक पीस डिस्क, सतह पीसने और किनारे के काम के लिए आदर्श।
प्रकार 29 (शंक्वाकार):आक्रामक स्टॉक हटाने और बेहतर सतह मिश्रण के लिए कोणीय डिजाइन।
प्रकार 1 (सीधा):कट-ऑफ अनुप्रयोगों के लिए उपयोग किया जाता है। यह सटीक कटिंग के लिए एक पतली प्रोफ़ाइल प्रदान करता है।
आवेदन पत्र:
पीसना:सामग्री हटाने और आकार देने के लिए मानक पीस डिस्क।
काटना:धातु को काटने के लिए कट-ऑफ व्हील का उपयोग करें, जिससे सीधा और साफ किनारा प्राप्त हो।
फ्लैप डिस्क:पीसने और फिनिशिंग को एक साथ मिलाएँ। सतहों को मिलाने और चिकना करने के लिए उपयुक्त।
ग्राइंडर के साथ संगतता:
सुनिश्चित करें कि पीसने वाली डिस्क इस्तेमाल की जा रही ग्राइंडर के प्रकार और गति के अनुकूल है। डिस्क के अधिकतम RPM (प्रति मिनट क्रांति) के लिए निर्माता की सिफारिशों की जाँच करें।
कार्य विशिष्टता:
भारी स्टॉक हटाना:कुशलतापूर्वक सामग्री हटाने के लिए मोटे ग्रिट और टाइप 27 या टाइप 29 डिस्क का चयन करें।
सतह परिष्करण:चिकनी फिनिश के लिए फ्लैप डिस्क के साथ मध्यम से बारीक ग्रिट का चयन करें।
सुरक्षा संबंधी विचार:
सुरक्षा दिशानिर्देशों का पालन करें, जिसमें उचित व्यक्तिगत सुरक्षा उपकरण (पीपीई) जैसे सुरक्षा चश्मा और दस्ताने पहनना शामिल है।
अधिक टिकाऊपन और सुरक्षा के लिए प्रबलित डिस्क चुनें।
ब्रांड और गुणवत्ता:
गुणवत्ता और स्थिरता के लिए जाने जाने वाले प्रतिष्ठित ब्रांडों से डिस्क चुनें। उच्च गुणवत्ता वाली डिस्क बेहतर प्रदर्शन और स्थायित्व प्रदान करती हैं।
लागत पर विचार:
ग्राइंडिंग डिस्क के अपेक्षित जीवनकाल और प्रदर्शन के साथ आरंभिक लागत को संतुलित करें। उच्च गुणवत्ता वाली डिस्क की आरंभिक लागत अधिक हो सकती है, लेकिन समय के साथ बेहतर मूल्य प्रदान कर सकती है।
इन कारकों पर विचार करके, ऑपरेटर अपने विशिष्ट अनुप्रयोगों के लिए सही ग्राइंडिंग डिस्क का चयन कर सकते हैं, जिससे दक्षता, सुरक्षा और इष्टतम परिणाम सुनिश्चित हो सकेंगे।
निष्कर्ष
निष्कर्ष में, उपयुक्त ग्राइंडिंग डिस्क का चयन सफल धातुकर्म और निर्माण परिणामों को प्राप्त करने का एक महत्वपूर्ण पहलू है। चुनाव विभिन्न कारकों पर निर्भर करता है जैसे कि जिस सामग्री पर काम किया जा रहा है, वांछित फिनिश और उपयोग में आने वाले ग्राइंडर का प्रकार। सामग्री संगतता, अपघर्षक प्रकार, ग्रिट आकार, पहिया प्रकार, अनुप्रयोग, ग्राइंडर संगतता, कार्य विशिष्टता, सुरक्षा, ब्रांड गुणवत्ता और लागत पर विचार करके, ऑपरेटर अपनी पीसने की प्रक्रियाओं में दक्षता और सुरक्षा बढ़ाने के लिए सूचित निर्णय ले सकते हैं।
सुरक्षा दिशा-निर्देशों का पालन करना, उचित व्यक्तिगत सुरक्षा उपकरण पहनना और ग्राइंडर और डिस्क संगतता के लिए निर्माता की सिफारिशों का पालन करना आवश्यक है। चाहे वह भारी स्टॉक हटाने, सतह की फिनिशिंग या कटिंग अनुप्रयोगों के लिए हो, सही ग्राइंडिंग डिस्क काम की गुणवत्ता और दक्षता को महत्वपूर्ण रूप से प्रभावित कर सकती है।
इसके अतिरिक्त, टूट-फूट के लिए समय-समय पर जांच, अधिक गर्मी और कंपन जैसी समस्याओं का समाधान, तथा लोडिंग समस्याओं को समझना, ग्राइंडिंग डिस्क के जीवन को बढ़ाने और निरंतर प्रदर्शन सुनिश्चित करने में योगदान देता है।
संक्षेप में, पीसने वाली डिस्क का चयन, उपयोग और रखरखाव करने के लिए एक अच्छी तरह से सूचित और व्यवस्थित दृष्टिकोण इष्टतम परिणाम प्राप्त करने, उत्पादकता बढ़ाने और सुरक्षित कार्य वातावरण सुनिश्चित करने के लिए महत्वपूर्ण है।
पोस्ट करने का समय: जनवरी-12-2024